Unique, practical, and effective! Our cold chain telematics system has been
customised for Schroeder Transport of Mecklenburg, Western Pomerania, resulting
in reliable refrigeration, optimal route navigation, and efficient driving
behaviour.
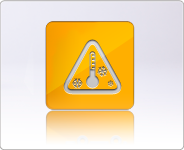
The tailored solution for the family-run transport company was created with not
only our proprietary software and hardware devices, but with a customised
formula of plugins and accessories that guarantees continuous refrigeration of
perishable goods, precise routing of delivery vehicles, and decreased fuel
consumption by monitoring driving behaviour.
As consumers, we take for granted the availability of fresh produce on
almost every street corner; moreover, it has become an expectation in our
everyday lives. This standard’s existence and maintenance is solely dependent
on today’s cold chain technology, a challenge for those organisations
responsible for the delivery of such goods. Fresh produce, as an idea, is an
amalgamation of various processes that can be brought together with telematics.
To achieve this, we at ENAiKOON have created a three-fold telematics solution
using messenger, temp-sensor, and can-66. This combination has allowed
Schroeder Transport to optimise their navigation, refrigeration, and driving
behaviour while creating new opportunities for expanding their business. The
collected data from the system is used by management only for the reports and
analysis related to cold chain, logistics, and fleet management.
Perfect Navigation: The ENAiKOON messenger
Schroeder Transport from Teterow, Germany, has equipped over 50 trucks and
40 refrigeraeted trailers with the cost effective telematics device
ENAiKOON locate-06. The high-performance locate-06 is responsible
for GPS and GPRS. It locates the trucks, transmits and receives their data, and
shows driving direction and speed. Schroeder Transport uses a navigation system
by Garmin that connects to the GPS device. The telematics web portal, inViu
pro, is linked to the navigation hardware along with the software plugin,
ENAiKOON messenger. This allows the dispatcher to create messages and new
driving destinations in the web portal and send them to the navigation
hardware. With the push of a button, the driver is able to simultaneously start
the route and begin the plugin’s guided information on the navigation system
for smooth execution of the driving routes. The navigation system transmits the
remaining distance and driving time to the web portal, keeping the dispatcher
up to date on the vehicle and trip status.
Cold Chain Transport: ENAiKOON temp-sensor
The key to cold chain is to know the ideal climate for fresh produce, and
every product has its own favourite temperature. Leafy vegetables, apples,
mangos, and pears all prefer different yet specific temperatures. Frozen fish
require a temperature of 18° C below zero (-40° F) and chocolate needs to be
kept at 18° C (64.4° F). There are always complexities when transporting such
goods and they begin with the vehicles. In the temperature-controlled
transports of Schroeder are two cooling chambers. These two chambers each have
a temperature sensor that is connected to the
ENAiKOON locate-04 telematics device. The
sensors measure the temperature, which is then sent to Schroeder’s
dispatchers through the locate-04. The freshness of their produce relies on the
fine tuning done by the drivers. Before the delivery, the drivers must select
what they are delivering using pre-configured buttons. Whether it is frozen
food or fresh meat, the content of the cargo and its status for delivery are
entered. These details are sent to the ENAiKOON system that configures the
temperature of the chambers. Thresholds and alarms are pre-programmed in the
system, which automates the control of temperatures and easing the process for
the drivers. Furthermore, it gives the estimated time for the cooling chambers
to reach their desired temperatures.
Economic driving: ENAiKOON can-66
For many years, the analysis of all vehicle system data from the vehicle’s
CAN-bus has fuelled our success. This has enabled our customers to objectively
compare individual driving styles and fuel consumption of different vehicles
and drivers in various categories. “We don’t want to compare apples to oranges,
our goal is rather to develop a fair evaluation for the driver,” says Jan
Schroeder, one of the two managing directors of the firm. The
can-66 works for long and short hauls, which is perfect for
Schroeder. The CAN-bus is a powerful tool that sends the user all important
information required for analysis. The web portal,
inViu
pro, is configured by us so that Schroeder receives a summary of important,
easy-to-read data. It can create groups and filters so that custom reports and
charts can be created; for example, reports can be created comparing long and
short hauls by fuel consumption, speed, and RPM. Schroeder utilises this in an
ambitious way: they have configured the data so that all drivers will be ranked
based on their fuel consumption. Whoever consumes more gas will be ranked lower
than those consuming less. They have implemented an incentive plan based on who
ranks the highest in hopes to motivate the drivers to use less fuel. Their goal
of a 10% decrease in fuel costs per driver through enhanced driving behaviour
is now within reach. Apply this to 50 long-haul trucks for a savings of almost
$ 300,000 per year – the cost of two new trucks.